Các bạn thân mến, chắc chúng ta nghe đến cụm từ lập trình PLC hay hệ thống PLC rồi đúng không ạ. Đây là một trong những lĩnh vực rất quan trọng trong công nghiệp đặc biệt là điều khiển, tự động hóa dây chuyền hay hệ thống. Hôm nay chúng tôi xin giới thiệu đến các bạn về PLC và lập trình PLC trong công nghiệp như thế nào các bạn nhé.
Tìm hiểu về PLC
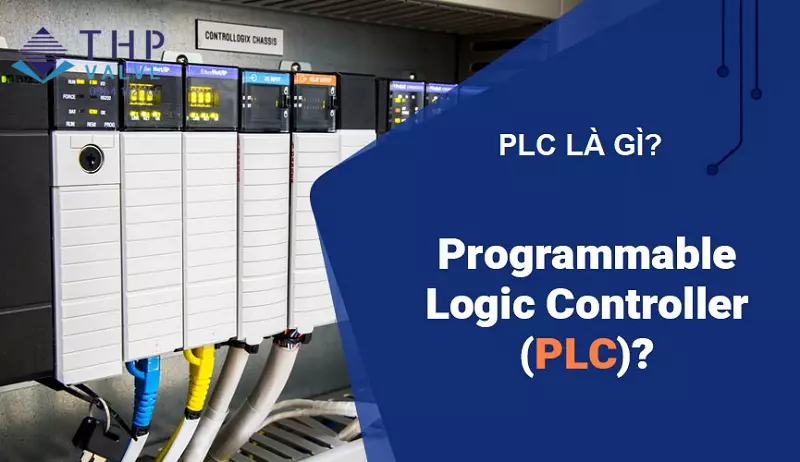
Định nghĩa PLC là gì?
PLC là viết tắt của “Programmable Logic Controller” (Bộ điều khiển logic có thể lập trình), là một thiết bị điện tử được sử dụng trong tự động hóa công nghiệp để kiểm soát và giám sát các hoạt động trong quá trình sản xuất.
PLC được thiết kế để thay thế các hệ thống điều khiển truyền thống dựa trên các bộ đếm, bộ giải mã, các điều khiển Relay hay các bộ vi xử lý đơn giản khác. Thiết bị này có khả năng lập trình được để xử lý các tín hiệu điện và điều khiển các động cơ, van, dây chuyền…. cảm biến và các thiết bị khác trong quá trình sản xuất.
PLC hoạt động dựa trên các chương trình điều khiển được lập trình trước đó và được cài đặt vào bộ nhớ của thiết bị. Khi PLC nhận được các tín hiệu từ các cảm biến hoặc từ các bộ đệm bên ngoài, chương trình điều khiển sẽ xử lý các tín hiệu này và đưa ra các tín hiệu điều khiển đến các thiết bị khác trong quá trình sản xuất.
Hệ thống lập trình PLC được sử dụng rộng rãi trong các ngành công nghiệp, chẳng hạn như sản xuất ô tô, sản xuất điện tử, chế biến thực phẩm và sản xuất dược phẩm. Với tính linh hoạt và khả năng tùy chỉnh cao, PLC đã giúp cho các quá trình sản xuất được thực hiện hiệu quả hơn và giảm thiểu các sai sót trong quá trình sản xuất.
Phát minh và quá trình phát triển của PLC
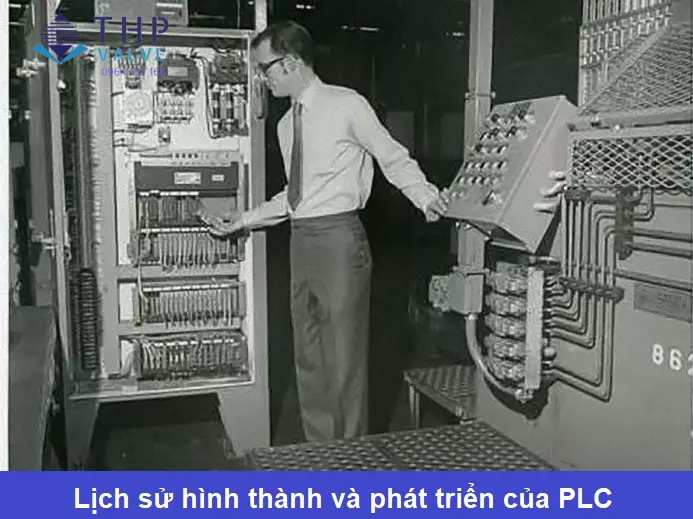
Phát minh PLC bắt đầu từ năm 1968, khi một kỹ sư người Mỹ tên là Dick Morley tìm ra một cách thức mới để kiểm soát các hệ thống sản xuất tự động. Ông Morley đã phát triển một hệ thống điều khiển dựa trên vi xử lý và lưu trữ bộ chương trình điều khiển trên bộ nhớ của máy tính.
Từ đó,hệ thống lập trình PLC đã trở thành công cụ quan trọng trong các ứng dụng tự động hóa công nghiệp và tiếp tục được phát triển trong suốt thập kỷ 1970 và 1980. PLC ngày nay đã trở thành một phần không thể thiếu của các hệ thống điều khiển tự động trong các ngành công nghiệp khác nhau, bao gồm sản xuất, năng lượng, hóa chất, dầu khí, thực phẩm và y tế.
Quá trình phát triển của PLC được chia thành ba thế hệ chính:
- Thế hệ đầu tiên: PLC được phát triển như một thiết bị rời khỏi bảng điều khiển để thay thế các bộ điều khiển dây thừng và bộ điều khiển điện tử cũ hơn. Thế hệ đầu tiên của PLC chủ yếu được sử dụng để thay thế các bộ điều khiển dây thừng và có tính ổn định và đáng tin cậy hơn.
- Thế hệ thứ hai: Thế hệ này đã thấy sự phát triển của các chức năng và tính năng mới, bao gồm khả năng truyền thông và điều khiển mạng, các tính năng xử lý tín hiệu phức tạp và khả năng lưu trữ dữ liệu. Các PLC thế hệ này đã được sử dụng rộng rãi trong các ứng dụng cần tính linh hoạt cao.
- Thế hệ thứ ba: Thế hệ này được phát triển để đáp ứng nhu cầu ngày càng tăng của các ứng dụng tự động hóa khắt khe và phức tạp. Các hệ thống lập trình PLC thế hệ này có thể xử lý các tác vụ phức tạp hơn, tốc độ xử lý nhanh hơn và khả năng tích hợp các hệ thống điều khiển nhỏ gọn hơn.
Hệ thống PLC và các thành phần của hệ thống PLC
Như chúng tôi đã nêu,hệ thống PLC (Programmable Logic Controller System) là một hệ thống tự động hóa công nghiệp, sử dụng các bộ vi xử lý để lập trình và điều khiển các quá trình sản xuất. Hệ thống này được thiết kế để thay thế các hệ thống điều khiển truyền thống dựa trên các bộ đếm, bộ giải mã, các điều khiển Relay hay các bộ vi xử lý đơn giản khác.
Một hệ thống PLC bao gồm các thành phần cơ bản sau:
- CPU (Central Processing Unit): Là trái tim của hệ thống PLC, chịu trách nhiệm xử lý các tín hiệu điều khiển và chương trình điều khiển được lập trình. CPU cũng có khả năng giao tiếp với các thiết bị ngoại vi khác của hệ thống.
- Memory (Bộ nhớ): Bộ nhớ lưu trữ chương trình điều khiển được lập trình cho hệ thống PLC. Bộ nhớ này được chia thành hai loại chính là bộ nhớ chương trình (Program Memory) và bộ nhớ dữ liệu (Data Memory).
- Input Modules (Module nhập liệu): Các module này được sử dụng để nhận các tín hiệu từ các cảm biến, các đầu vào analog(Đồng hồ đo lưu lượng điện từ, van điều khiển điện tuyến tính, van điều khiển khí nén…) hoặc các đầu vào kỹ thuật số. Chúng chuyển đổi các tín hiệu này thành các tín hiệu điện để xử lý trong hệ thống PLC.
- Output Modules (Module xuất liệu): Các module này được sử dụng để điều khiển các thiết bị xuất liệu như động cơ, van điều khiển, đèn, dây chuyển sản xuất… và các thiết bị khác. Chúng chuyển đổi các tín hiệu điện từ CPU thành các tín hiệu điều khiển để điều khiển các thiết bị này.
- Power Supply (Nguồn điện): Là nguồn cung cấp điện cho toàn bộ hệ thống PLC. Nguồn điện này có thể được cung cấp từ nguồn AC hoặc DC.
- Communication Interface (Giao tiếp): Các giao diện này được sử dụng để kết nối các thiết bị ngoại vi khác với hệ thống PLC, chẳng hạn như các thiết bị đầu cuối, máy tính và các thiết bị khác.
Tất cả các thành phần này được kết hợp với nhau để tạo thành một hệ thống tự động hóa công nghiệp hoàn chỉnh. Khi hệ thống được cấu hình và chúng ta gọi là lập trình PLC đúng cách, nó có thể giúp cho các quá trình sản xuất được thực hiện hiệu quả hơn và giảm thiểu các sai sót
Nguyên lý hoạt động của một hệ thống PLC
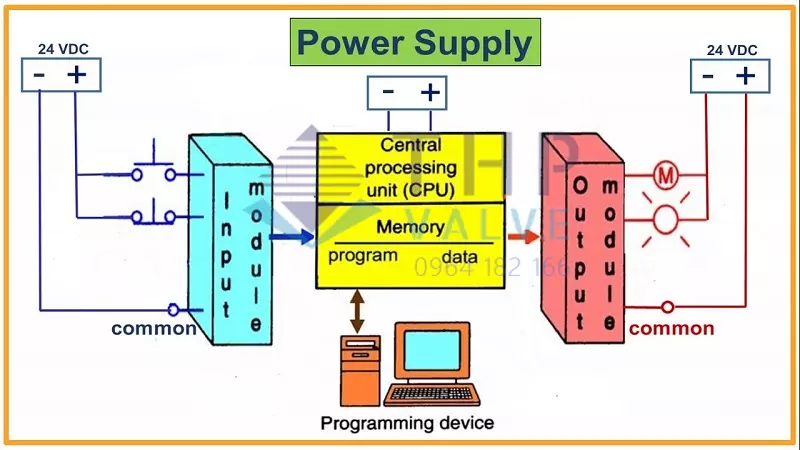
Để thiết kế một hệ thống lập trình PLC là vô cùng phức tạp.Đây là một hệ thống tự động hóa công nghiệp sử dụng các bộ vi xử lý để lập trình và điều khiển các quá trình sản xuất. Nguyên lý hoạt động cơ bản của một hệ thống PLC là nhận các tín hiệu đầu vào từ các cảm biến, xử lý thông tin và tạo ra các tín hiệu điều khiển để điều khiển các thiết bị đầu ra.
Một hệ thống được lập trình PLC sẽ hoạt động theo nguyên lý vận hành cụ thể như sau:
Bước 1: Thu thập tín hiệu đầu vào:
Các tín hiệu đầu vào bao gồm các thông tin về trạng thái hoặc giá trị của các thiết bị trong quá trình sản xuất, chẳng hạn như nhiệt độ, áp suất, mức độ, vị trí đóng mở(Các loại van điều khiển điện, van điều khiển khí nén, cảm biến…) và tốc độ. Những tín hiệu này được thu thập bởi các cảm biến, tín hiệu gửi về và gửi đến các module đầu vào của hệ thống PLC để xử lý.
Bước 2:
Xử lý tín hiệu: CPU (Central Processing Unit) của hệ thống PLC nhận tín hiệu đầu vào và xử lý chúng. Việc xử lý tín hiệu bao gồm các bước sau:
- Tiền xử lý: Các tín hiệu đầu vào được chuyển đổi sang dạng số học để có thể được xử lý bởi CPU.
- Lưu trữ: Các tín hiệu đầu vào được lưu trữ trong bộ nhớ của hệ thống PLC để sử dụng trong quá trình xử lý.
- Xử lý logic: CPU sử dụng các chương trình điều khiển được lập trình PLC trước để xử lý các tín hiệu đầu vào. Các chương trình này có thể là các phép toán logic đơn giản hoặc các chương trình phức tạp hơn, tùy thuộc vào yêu cầu của quá trình sản xuất hoặc yêu cầu của hệ thống vận hành
Bước 3: Tạo ra tín hiệu điều khiển
Sau khi xử lý tín hiệu đầu vào, CPU tạo ra các tín hiệu điều khiển để điều khiển các thiết bị đầu ra. Các tín hiệu điều khiển này được tạo ra bằng cách sử dụng các chương trình điều khiển được lập trình trước.
Bước 4: Điều khiển thiết bị đầu ra
Các tín hiệu điều khiển được gửi đến các module đầu ra của hệ thống PLC để điều khiển các thiết bị đầu ra, chẳng hạn như động cơ, van PID(van điều khiển điện, van điều khiển khí nén), đèn, quạt, dây chuyền tự động… và các thiết bị khác. Các tín hiệu này được chuyển đổi sang dạng tương ứng với các thiết bị đầu ra để điều khiển chúng.
Bước 5: Lặp lại quá trình
Quá trình này được lặp lại liên tục để giám sát và điều khiển các quá trình sản xuất trong thời gian thực. Các tín hiệu đầu vào được liên tục thu thập, xử lý và điều khiển các thiết bị đầu ra để đảm bảo
>>>Có thể bạn quan tâm: PID là gì?
Tại sao lập trình PLC quan trọng cho ngành công nghiệp?
Lập trình PLC là một phần quan trọng trong ngành công nghiệp tự động hóa. Điều này bởi vì PLC cung cấp cho các nhà sản xuất khả năng điều khiển, giám sát và tự động hóa các quy trình sản xuất. Dưới đây là một số lý do tại sao hệ thống PLC quan trọng cho ngành công nghiệp:
- Tăng năng suất và hiệu quả sản xuất: PLC giúp tăng năng suất và hiệu quả sản xuất bằng cách giảm thời gian chết và tối ưu hóa quy trình sản xuất. Với khả năng điều khiển các thiết bị công nghiệp, Hệ thống được lập trình PLC có thể giúp giảm thiểu sai sót trong quy trình sản xuất và tăng độ chính xác và độ tin cậy của các hệ thống.
- Giảm chi phí sản xuất: Các hệ thống PLC có thể giúp giảm chi phí sản xuất bằng cách tối ưu hóa quy trình sản xuất và giảm thời gian chết. Điều này giúp giảm chi phí nhân công và tăng năng suất, đồng thời giảm thiểu sự cố và thời gian bảo trì của các thiết bị.
- Đảm bảo an toàn: Các hệ thống PLC có thể được sử dụng để giám sát các thiết bị công nghiệp và đảm bảo an toàn cho công nhân, nhân viên kỹ thuật. PLC có thể giảm thiểu nguy cơ tai nạn do sai sót hoặc sự cố thiết bị trong quy trình sản xuất.
- Điều khiển quy trình sản xuất: Các hệ thống điều khiển bằng lập trình PLC có thể được sử dụng để điều khiển quy trình sản xuất, bao gồm đo lường và kiểm soát nhiệt độ, áp suất, lưu lượng, và các thông số quan trọng khác. Điều này giúp đảm bảo chất lượng sản phẩm được kiểm soát và tối ưu hóa quy trình sản xuất.
- Tự động hóa quy trình sản xuất: Các hệ thống PLC có thể được sử dụng để tự động hóa quy trình sản xuất. Với khả năng lưu trữ chương trình điều khiển, các hệ thống PLC có thể tự động hóa quy trình sản xuất mà không cần sự can thiệp của nhân công vận hành thủ công, giảm chi phí và tăng hiệu quả sản xuất.
- Dễ dàng sửa chữa và bảo trì: PLC được thiết kế để dễ dàng sửa chữa và bảo trì hơn so với các hệ thống điện tử khác. Với khả năng ghi nhớ chương trình điều khiển, lập trình PLC giúp các nhân viên kỹ thuật, nhân viên vận hành có thể nhanh chóng xác định và khắc phục sự cố khi xảy ra.
- Tính linh hoạt: PLC có thể được cấu hình để phục vụ nhiều ứng dụng khác nhau trong ngành công nghiệp, từ quy trình sản xuất đơn giản đến các hệ thống phức tạp.
- Tương thích với các hệ thống khác: PLC có thể được tích hợp với các hệ thống khác trong quy trình sản xuất, bao gồm các thiết bị cảm biến, bộ điều khiển nhiệt độ, máy tính, hệ thống giám sát và kiểm soát quy trình.
- Hỗ trợ quy trình sản xuất linh hoạt: Với khả năng lập trình linh hoạt, các hệ thống PLC có thể được sử dụng để hỗ trợ quy trình sản xuất linh hoạt và tối ưu hóa quy trình sản xuất trong một môi trường sản xuất đa dạng.
- Đáp ứng yêu cầu tiêu chuẩn chất lượng: PLC có khả năng kiểm soát và giám sát các thông số quan trọng trong quy trình sản xuất, đảm bảo chất lượng sản phẩm đáp ứng tiêu chuẩn chất lượng yêu cầu.
Những yếu tố cần quan tâm khi lập trình PLC
Ngôn ngữ lập trình PLC phổ biến hiện nay
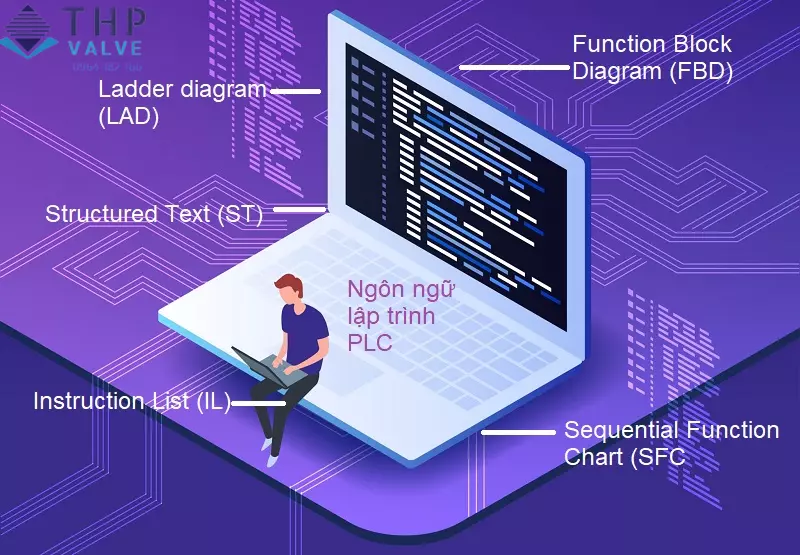
Ngôn ngữ lập trình PLC Ladder diagram (LAD)
Đây là một trong những ngôn ngữ lập trình PLC phổ biến nhất và dễ sử dụng nhất. Nó được thiết kế để giống như các mạch điện dây rối truyền thống với các relay và các thiết bị điện tử khác.
Ladder diagram sử dụng các biểu tượng đại diện cho các thành phần điện tử, chẳng hạn như relay, bobin, cảm biến, van, motor và các chức năng logic khác. Các biểu tượng này được nối với nhau bằng các đường dây để tạo ra các chương trình logic kiểm soát. Biểu đồ xếp hạng được sắp xếp theo các cột dọc tượng trưng cho các đường dây, trong đó các biểu tượng được sắp xếp theo thứ tự từ trái sang phải.
Các đường dây được chia thành hai loại: đường dây đầu vào (input) và đường dây đầu ra (output). Đường dây đầu vào thường được kết nối với các cảm biến và thiết bị đầu vào khác để kiểm tra trạng thái của chúng. Các đường dây đầu ra được kết nối với các thiết bị đầu ra, chẳng hạn như van, motor, bóng đèn, v.v., để điều khiển chúng.
Ladder diagram rất phổ biến vì nó dễ hiểu và dễ sử dụng cho các kỹ sư và kỹ thuật viên điều khiển. Nó cũng có thể được sử dụng để mô tả các quy trình kiểm soát phức tạp. Tuy nhiên, nó có một số hạn chế như khó thực hiện các chức năng phức tạp hơn, khó quản lý với các chương trình lớn, và khó phát hiện các lỗi khi chương trình có kích thước lớn.
Ngôn ngữ lập trình Function Block Diagram (FBD).
Function Block Diagram (FBD) là một trong những ngôn ngữ lập trình PLC phổ biến và được sử dụng rộng rãi. Nó được thiết kế để trình bày các hàm logic và quy trình điều khiển bằng các khối hàm được nối với nhau.
FBD sử dụng các khối hàm để biểu diễn các phép toán logic và các hành động điều khiển khác. Các khối hàm này có thể là các phép toán logic cơ bản như AND, OR, NOT, hoặc là các hàm điều khiển phức tạp hơn như hàm PID (Proportional-Integral-Derivative) hoặc hàm điều khiển định vị. Các khối hàm được kết nối với nhau bằng các đường dây để tạo ra các chương trình logic kiểm soát.
Các đường dây được chia thành hai loại: đường dây đầu vào và đường dây đầu ra. Các đường dây đầu vào thường được kết nối với các cảm biến và thiết bị đầu vào khác để kiểm tra trạng thái của chúng. Các đường dây đầu ra được kết nối với các thiết bị đầu ra, chẳng hạn như van, motor, bóng đèn, v.v., để điều khiển chúng.
FBD có thể được sử dụng để mô tả các quy trình kiểm soát phức tạp và là một trong những ngôn ngữ lập trình phổ biến được sử dụng trong các ứng dụng công nghiệp. FBD có một số ưu điểm, chẳng hạn như dễ dàng để đọc và hiểu, quản lý chương trình tốt hơn trong các chương trình lớn, và có thể thực hiện các chức năng phức tạp hơn. Tuy nhiên, nó cũng có một số hạn chế như khó kiểm tra và phát hiện lỗi trong các chương trình phức tạp.
Ngôn ngữ lập trình Structured Text (ST)
Đây là một dạng ngôn ngữ lập trình được sử dụng cho các ứng dụng yêu cầu độ logic và phức tạp có tính tái sử dụng cao. Đòi hỏi hệ thống và xử lý các bước cao hơn so với các ngôn ngữ ở trên.
ST được thiết kế để giúp lập trình viên tạo ra các chương trình logic phức tạp và dễ dàng quản lý chúng. ST có cú pháp tương tự như các ngôn ngữ lập trình khác như C hoặc Pascal, với các khai báo biến, các lệnh điều khiển, các vòng lặp và các cấu trúc điều kiện.
ST cho phép lập trình viên viết các hàm tùy chỉnh và sử dụng lại chúng trong nhiều chương trình khác nhau. Điều này giúp tiết kiệm thời gian và nỗ lực trong việc phát triển chương trình.
ST cũng cho phép lập trình viên thực hiện các tính toán phức tạp và sử dụng các công cụ như hàm số, các phép toán số học, logic và chuỗi, các lệnh điều khiển vòng lặp và các cấu trúc điều kiện.
Mặc dù ST có thể có độ phức tạp cao hơn so với các ngôn ngữ lập trình khác, nhưng nó cũng có nhiều ưu điểm như khả năng thực hiện các chức năng phức tạp hơn, sử dụng lại các chương trình dễ dàng hơn và tính linh hoạt cao hơn trong việc phát triển các chương trình kiểm soát.
Ngôn ngữ lập trình Instruction List (IL)
Instruction List (IL) là một trong những ngôn ngữ lập trình PLC cơ bản và phổ biến. Nó được sử dụng để biểu diễn chương trình dưới dạng danh sách các lệnh hoạt động.
IL được thiết kế để giúp lập trình viên viết chương trình một cách đơn giản và hiệu quả. Ngôn ngữ này sử dụng các chỉ thị và toán tử để thực hiện các hoạt động logic và kiểm soát các thiết bị.
Các lệnh trong IL được liệt kê trong một danh sách, mỗi lệnh bao gồm một mã lệnh và các tham số đi kèm. Mã lệnh chỉ ra loại hoạt động cần thực hiện, trong khi các tham số cung cấp thông tin cần thiết để thực hiện hoạt động đó.
IL thường được sử dụng trong các ứng dụng đơn giản và có tính chất thời gian thực, nơi các chức năng kiểm soát cơ bản được thực hiện nhanh chóng và hiệu quả. Tuy nhiên, IL không thích hợp cho các chương trình phức tạp và khó bảo trì, vì danh sách các lệnh có thể trở nên rất dài và khó đọc.
Ngôn ngữ lập trình PLC: Sequential Function Chart (SFC)
Sequential Function Chart (SFC) là một trong những ngôn ngữ lập trình PLC dựa trên khái niệm của các biểu đồ hoạt động (operation chart). Nó được sử dụng để mô tả quá trình điều khiển các thiết bị trong hệ thống.
SFC thường được sử dụng để lập trình các quy trình liên tục, có nghĩa là các hoạt động sẽ được thực hiện theo một trình tự nhất định. SFC bao gồm các khối chức năng (function blocks) được sắp xếp theo dạng cây nhị phân, trong đó các khối chức năng có thể chứa các khối con khác.
SFC cung cấp một phương tiện trực quan để mô tả các quá trình điều khiển. Các khối chức năng và các liên kết giữa chúng có thể được biểu diễn bằng các biểu đồ dạng hình chữ nhật và các mũi tên để đại diện cho các điều kiện logic và các hoạt động.
Các khối chức năng trong SFC có thể thực hiện các hoạt động logic, tính toán và điều khiển các thiết bị. Nó cũng cho phép lập trình viên xác định các trạng thái của hệ thống và các điều kiện để chuyển đổi giữa các trạng thái đó.
Cách chọn ngôn ngữ lập trình PLC phù hợp cho mục đích sử dụng
- Ứng dụng và mục đích sử dụng: Một số ứng dụng và mục đích sử dụng như kiểm soát đơn giản, phát triển nhanh chóng hoặc lập trình theo hướng hướng đối tượng sẽ phù hợp với một ngôn ngữ nhất định.
- Kiến thức và kinh nghiệm của nhà lập trình: Kiến thức và kinh nghiệm của lập trình viên trong một ngôn ngữ cụ thể cũng quan trọng để chọn ngôn ngữ phù hợp.
- Khả năng hỗ trợ của nhà sản xuất PLC: Một số nhà sản xuất PLC có thể chỉ hỗ trợ một số ngôn ngữ lập trình cụ thể.
- Tính sẵn có của tài liệu và nguồn lực: Tính sẵn có của tài liệu và nguồn lực cũng là một yếu tố quan trọng trong việc chọn ngôn ngữ lập trình phù hợp.
Dưới đây là một số lời khuyên để chọn ngôn ngữ lập trình phù hợp với mục đích sử dụng:
- Nếu cần lập trình nhanh chóng, Ladder Diagram (LD) và Function Block Diagram (FBD) là hai ngôn ngữ phổ biến được sử dụng trong ngành công nghiệp để phát triển các ứng dụng đơn giản và hiệu quả.
- Nếu bạn muốn lập trình kiểu đối tượng, có tính tái sử dụng cao, thì Structured Text (ST) là một lựa chọn tốt.
- Nếu bạn đang làm việc với các chương trình có tính trực quan cao, cần một cách hiển thị đồ họa rõ ràng, Sequential Function Chart (SFC) là một ngôn ngữ lập trình phù hợp.
- Instruction List (IL) là một ngôn ngữ lập trình được sử dụng khi cần lập trình tối ưu hóa và định dạng thấp hơn. Tuy nhiên, nó khó để đọc và bảo trì hơn các ngôn ngữ khác.
Các bước cơ bản để lập trình PLC
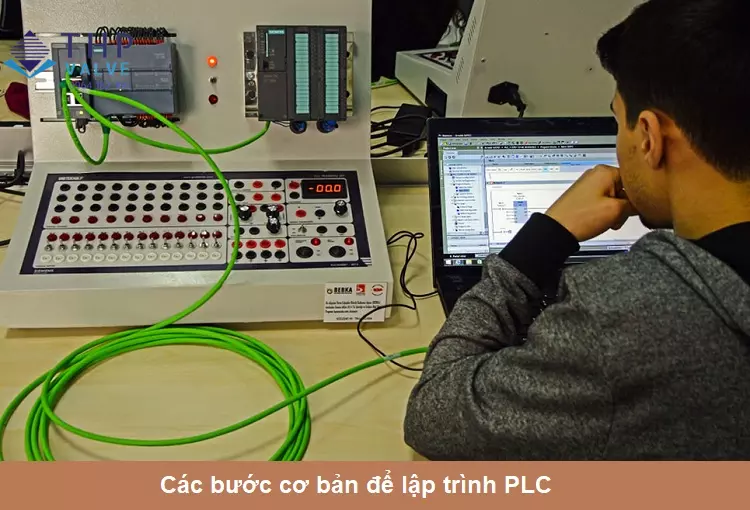
Bước 1: Xác định yêu cầu hệ thống: Trước khi bắt đầu lập trình, bạn cần phải hiểu rõ yêu cầu của hệ thống, bao gồm các chức năng, đầu vào và đầu ra cần sử dụng.
Bước 2: Thiết kế chương trình: Sau khi đã xác định yêu cầu, bạn cần thiết kế chương trình để thực hiện chức năng cần thiết. Đây là quá trình quan trọng, nên bạn nên có kế hoạch cẩn thận trước khi bắt đầu.
Bước 3: Lựa chọn ngôn ngữ lập trình: Sau khi đã thiết kế chương trình, bạn cần lựa chọn ngôn ngữ lập trình phù hợp để triển khai chương trình. Tùy vào yêu cầu của chương trình hay của hệ thống mà bạn chọn ngôn ngữ phù hợp
Bước 4: Viết mã lệnh: Bước này bao gồm viết mã lệnh cho chương trình, sử dụng ngôn ngữ lập trình đã chọn. Nên sử dụng các lệnh và cấu trúc phù hợp để đảm bảo tính đúng đắn và hiệu quả của chương trình.
Bước 5: Kiểm tra và sửa lỗi: Sau khi viết xong chương trình, bạn cần kiểm tra chương trình để đảm bảo tính đúng đắn và hoạt động đúng như mong đợi. Nếu phát hiện lỗi, bạn cần sửa chúng để chương trình hoạt động tốt.
Bước 6: Tải chương trình vào PLC: Khi chương trình đã hoàn thành, bạn cần tải chương trình vào PLC để chạy chương trình.
Bước 7: Kiểm tra hoạt động: Sau khi đã tải chương trình vào PLC, bạn cần kiểm tra hoạt động của chương trình trên hệ thống thực tế. Nếu có lỗi, bạn cần sửa chúng để đảm bảo hoạt động đúng như mong đợi.
Phần mềm lập trình PLC Delta
Giới thiệu chung PLC Delta
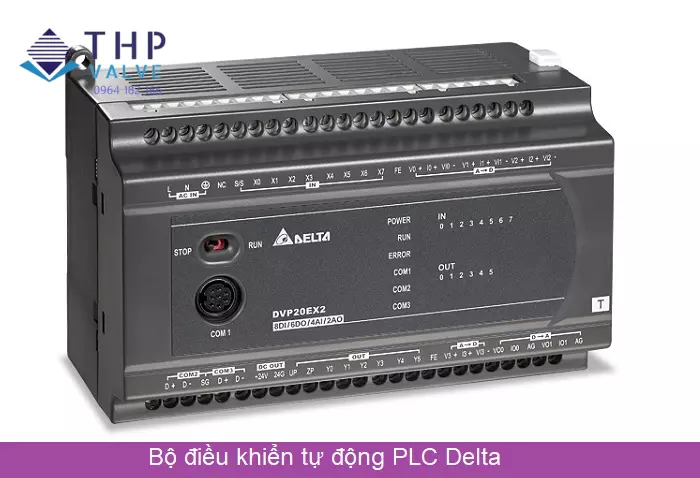
PLC Delta là bộ điều khiển PLC, được sản xuất bởi tập đoàn Delta Electronics, một công ty đa quốc gia của Đài Loan. PLC Delta được thiết kế để kiểm soát và giám sát các quá trình sản xuất và tự động hóa trong các ngành công nghiệp khác nhau, bao gồm công nghiệp điện tử, ô tô, thực phẩm và đồ uống, dược phẩm, và nhiều lĩnh vực khác.
PLC Delta có nhiều tính năng và ưu điểm, bao gồm khả năng xử lý nhanh, khả năng kết nối với nhiều thiết bị khác nhau, tính linh hoạt và dễ sử dụng. Nó cũng có khả năng điều khiển các quá trình phức tạp, cung cấp độ chính xác cao và tiết kiệm năng lượng, giảm chi phí sản xuất và tăng hiệu suất sản xuất.
PLC Delta có nhiều loại và dòng sản phẩm khác nhau, phù hợp với nhiều ứng dụng khác nhau, từ các ứng dụng cơ bản đến các ứng dụng phức tạp. Các sản phẩm của Delta được bảo đảm chất lượng cao và đáp ứng được nhu cầu đa dạng của khách hàng trong các lĩnh vực khác nhau.
Phần mềm lập trình PLC Delta
Ngày nay, mọi thứ đơn giản và dễ dàng hơn nhiều với việc sử dụng phần mềm PLC Delta để lập trình điều khiển cho các hệ thống tự động hóa trong công nghiệp. Phần mềm lập trình PLC Delta được viết ra chính là để điều khiển các thiết bị tự động hóa trong hệ thống PLC.
Phần mềm lập trình PLC Delta là một công cụ cho phép người dùng lập trình và cấu hình các bộ điều khiển logic programable (PLC) của Delta Electronics. Phần mềm này được thiết kế để đơn giản hóa quá trình lập trình và cấu hình PLC Delta, giúp người dùng tối ưu hóa hiệu suất và nâng cao tính ổn định của hệ thống tự động hóa.
PLC Delta hỗ trợ nhiều loại phần mềm lập trình, bao gồm DVP Suite, WPLSoft, ISPSoft và tùy chọn khác. Mỗi phần mềm có đặc điểm và chức năng khác nhau để phù hợp với các ứng dụng và mục đích sử dụng khác nhau.
Với phần mềm lập trình PLC Delta, người dùng có thể thiết kế và lập trình các chương trình điều khiển PLC Delta với các ngôn ngữ lập trình như Ladder, Function Block Diagram (FBD), Instruction List (IL) và Structured Text (ST). Ngoài ra, phần mềm này cũng cung cấp nhiều tính năng tiện ích như mô phỏng và kiểm tra chương trình, giúp người dùng tiết kiệm thời gian và nâng cao độ chính xác của chương trình.
Link Tải phần mềm Lập trình PLC Delta mới nhất 2023
Ứng dụng của hệ thống lập trình PLC
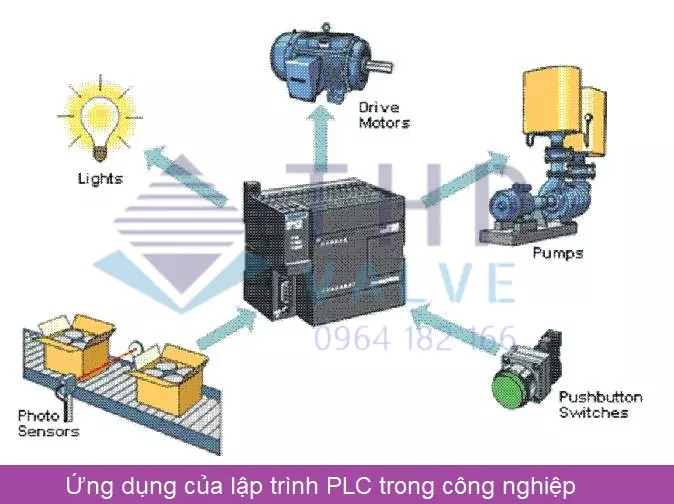
- Điều khiển hệ thống sản xuất: PLC được sử dụng để điều khiển các quy trình sản xuất trong ngành công nghiệp, bao gồm cả quá trình sản xuất trong các nhà máy, nhà xưởng, phân xưởng, nhà kho, và hệ thống dây chuyền sản xuất. Hệ thống PLC có thể kiểm soát các quy trình sản xuất, bao gồm cả quá trình tiếp nhận nguyên liệu, sản xuất và đóng gói sản phẩm.
- Hệ thống điều khiển thang máy: Hệ thống PLC được sử dụng để điều khiển các thang máy trong tòa nhà. PLC có thể giám sát tất cả các tín hiệu và mức độ trong thang máy để đảm bảo an toàn cho người sử dụng.
- Hệ thống điều khiển hệ thống HVAC: Hệ thống HVAC là hệ thống điều hòa không khí, thông gió và điều hòa nhiệt độ trong tòa nhà.Lập trình PLC được sử dụng để kiểm soát các hệ thống HVAC, bao gồm cả việc điều chỉnh nhiệt độ, độ ẩm và lưu lượng không khí.
- Hệ thống điều khiển tàu thủy: PLC được sử dụng trong hệ thống điều khiển tàu thủy để giám sát các thông số, bao gồm cả tốc độ, hướng đi và các thông số liên quan đến động cơ và hệ thống năng lượng.
- Hệ thống điều khiển bảo mật: PLC được sử dụng trong các hệ thống bảo mật để giám sát và điều khiển các thiết bị bảo mật, bao gồm cả hệ thống giám sát, hệ thống chữa cháy, hệ thống báo động và hệ thống quản lý truy cập.
- Hệ thống điều khiển thực phẩm và đồ uống: PLC được sử dụng trong hệ thống sản xuất thực phẩm và đồ uống để giám sát và điều khiển các quy trình sản xuất, bao gồm cả việc tiếp nhận nguyên liệu, xử lý và đóng gói sản phẩm.
- Hệ thống đóng/mở và kiểm soát năng lượng: sử dụng hệ thống lập trình PLC để điều khiển các thiết bị đóng/mở như van điều khiển, máy bơm, điều hòa, máy sấy…, quản lý năng lượng tiêu thụ và tối ưu hóa hiệu suất hoạt động của hệ thống.
- Hệ thống an toàn và bảo vệ: sử dụng PLC để kiểm soát các hệ thống an toàn và bảo vệ như hệ thống chữa cháy, hệ thống phát hiện khí độc, hệ thống báo động và giám sát an ninh.
- Hệ thống điều khiển thông minh trong tòa nhà: sử dụng PLC để kiểm soát các hệ thống thông gió, hệ thống chiếu sáng, hệ thống điều hòa không khí và các hệ thống khác trong tòa nhà.
- Hệ thống kiểm soát và quản lý trong các ngành công nghiệp khác: Hệ thống lập trình PLC cũng được sử dụng trong các ứng dụng khác như trong lĩnh vực nước và môi trường, hệ thống điều khiển trong công nghiệp dược phẩm, thực phẩm và nhiều ngành công nghiệp khác.
Trên đây là toàn bộ nội dung bài viết về lập trình PLC của chúng tôi. Bài viết đã giới thiệu qua cho các bạn biết được PLC là gì? Hệ thống PLC bao gồm những thành phần gì
Cùng với đó chúng tôi cũng đã giới thiệu về các ngôn ngữ dùng cho hệ thống lập trình PLC hiện nay. Những ưu điểm khi sử dụng hệ thống PLC.
Có thể nói rằng, hệ thống PLC hay lập trình PLC cho các hệ thống công nghiệp tự động cần phải có kiến thức và kinh nghiệm. Bài viết cũng chỉ mang tính khái quát chung, phạm vi nội dung có hạn, không thể triển khai chi tiết thêm
Cảm ơn các bạn đã quan tâm và theo dõi bài viết, hẹn gặp lại ở các bài viết sau!